Wesentliche in der Stahlerzeugung anfallende Luftschadstoffe sind neben Treibhausgasen (insbesondere CO2) Schwefeldioxid (SO2), Stickoxide (NOx) und Staub. Bei allen diesen Emissionen werden die gesetzlich vorgeschriebenen Grenzwerte gesichert eingehalten. Die Messung dieser Parameter und die Erhebung von deren Jahresfrachten erfolgen über kontinuierliche Messungen sowie diskontinuierliche Untersuchungen.
Die voestalpine ist bemüht, Luftschadstoffe, die während der Produktion aus rein prozesstechnischen Gründen entstehen, so weit als möglich zu minimieren. Dies gelingt einerseits über laufende technische Prozessoptimierungen (PI-Maßnahmen, process integrated measures) und andererseits durch Nachsorgeeinrichtungen am letzten Stand der Technik, die verbleibende Emissionen vermindern (End-of-Pipe-Maßnahmen).
Grundsätzlich sind prozessbedingte Emissionen, die vor allem aus erforderlichen Rohstoffen und bestehenden Herstellungsverfahren resultieren, aufgrund technologischer Grenzen nicht vollständig vermeidbar. Dank der bereits Mitte der 1980er-Jahre begonnenen und seitdem mit erheblichem technischen und finanziellen Aufwand kontinuierlich weiterverfolgten Umweltschutzmaßnahmen konnte das Emissionsniveau auf ein technologisch erreichbares Minimum gesenkt werden. Mit den angewandten Technologien ist somit keine weitere signifikante Verringerung möglich, was sich vor allem auch in den nachfolgenden Darstellungen zeigt. Beispielsweise liegen die spezifischen Emissionen für CO2, SO2 und NOx in den letzten fünf Jahren innerhalb der produktionsbedingten Schwankungsbreite. Betrachtet man die vergangenen drei Jahrzehnte, so wurden die spezifischen Emissionen des voestalpine-Konzerns (d.h. bezogen auf eine Tonne Rohstahl) bei CO2 um 20 %, bei SO2 um 75 %, bei NOx um 27 % und bei Staub um 95 % reduziert.
CO2-Emissionen
Bei der Rohstahlproduktion im LD-Verfahren, das nach wie vor weltweiter Standard der Stahlherstellung ist, entstehen CO2-Emissionen aus unvermeidbaren, prozessbedingten chemischen Reaktionen. Die Rohstoffe Kohle/Koks werden in der Roheisenerzeugung im Hochofen als Reduktionsmittel benötigt; Kohlenstoff ist erforderlich, um dem Eisenerz den Sauerstoff zu entziehen. Weiters wird anschließend durch Einblasen von Sauerstoff im LD-Konverter der im Roheisen noch enthaltene Kohlenstoff oxidiert. Aus der Verbindung von Kohlenstoff und Sauerstoff resultiert somit Kohlendioxid (CO2).
Eine Reduzierung dieser prozessbedingten CO2-Emissionen kann also nur durch teilweisen bzw. (im Falle einer vollständigen Entkarbonisierung) gänzlichen Ersatz von Kohlenstoff und damit völlig neue Herstellungsverfahren erreicht werden. (Siehe dazu auch das Kapitel „Energie- und Klimapolitik“.) Diese technologischen Optionen sind aufgrund ihrer Komplexität aus heutiger Sicht jedoch erst längerfristig realisierbar.
Wie einleitend dargestellt, liegen der erforderliche Einsatz von Kohlenstoff und die daraus resultierenden CO2-Emissionen bereits sehr nahe am technisch möglichen Minimum.
An den Standorten Linz und Donawitz, deren Hochöfen im europäischen Vergleich zu den besten Anlagen gehören, wurden 2015 insgesamt 11,7 Mio. t CO2 emittiert. Dies entspricht spezifischen CO2-Emissionen (bezogen auf eine Tonne Rohstahl) von 1,67 t. Die Veränderungen liegen gegenüber den Vergleichswerten innerhalb der produktionsbedingten Schwankungsbreite.
Spezifische CO2-Emissionen der voestalpine gemäß EZG
in t/t Rohstahl
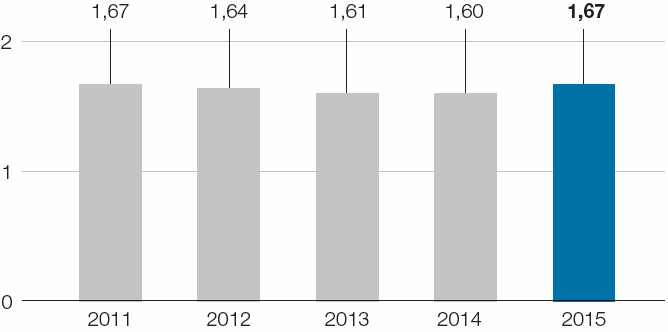
Emissionen der Standorte Linz und Donawitz gemäß Emissionszertifikategesetz (EZG)
Hochqualitätsstahl leistet über seine Anwendungen (etwa Leichtbau, verbesserter Wirkungsgrad in Kraftwerken, Elektromotoren, erneuerbare Energien) einen erheblichen Beitrag zu einer Verbesserung der Energie- und damit der CO2-Bilanz dieser Produkte. Laut einer Studie der Boston Consulting Group im Auftrag der Wirtschaftsvereinigung Stahl („CO2-Bilanz Stahl – ein Beitrag zum Klimaschutz“) wird über diese Anwendungen durchschnittlich sechsmal so viel CO2 eingespart wie in der Stahlproduktion entsteht.
Auszeichnungen für Klimaschutz
Unser Produktionsstandort Zeltweg produziert bereits seit 2010 CO2-neutral und wurde mit dem European EMAS Award 2014 für eco-innovations ausgezeichnet. Neben Maßnahmen zur Effizienzsteigerung und Verbrauchsvermeidung wurde die Werksbeheizung zu 75 % auf Biomasse umgestellt und ein Kleinwasserkraftwerk an der Pöls installiert. Die voestalpine Tubulars GmbH & Co KG in Kindberg wurde für ihre umfassende Kompetenz im Klimaschutz, speziell in Sachen Energieeffizienz, vom österreichischen Lebensministerium mit dem klimaaktiv-Preis ausgezeichnet.
voestalpine Polynorm B.V., Niederlande
Durch neue Kompressoren mit Wärmerückgewinnungssystem können künftig pro Jahr fast 50.000 m3 Erdgas und damit mehr als 340.000 t CO2 eingespart werden.
Spezifische SO2-Emissionen
in kg/t Rohstahl
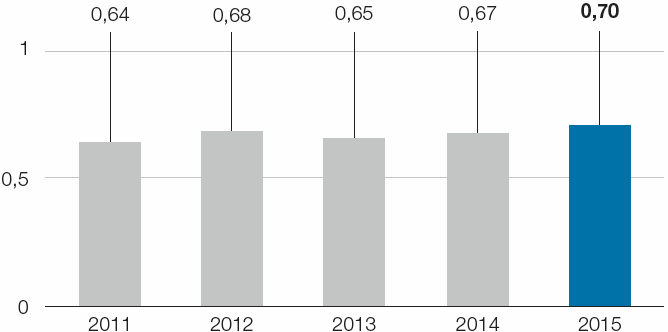
SO2-Emissionen
Schwefel ist in Rohstoffen enthalten und wird über diese in den Produktionsprozess eingebracht. In bestimmten Verarbeitungsschritten sowie bei der energetischen Verwertung von Kuppelprodukten (Kokereigas und Gichtgas) wird er als Schwefeldioxid (SO2) freigesetzt.
Die spezifischen SO2-Emissionen lagen 2015 bei 0,70 kg je Tonne Rohstahl. Die Veränderungen in den letzten Jahren liegen innerhalb der produktionsbedingten Schwankungsbreite.
Spezifische NOX-Emissionen
in kg/t Rohstahl
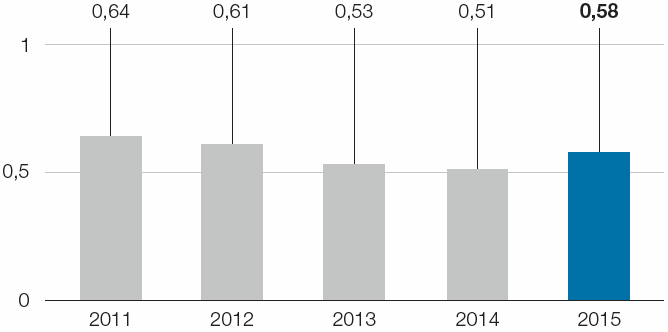
NOx-Emissionen
Stickstoffoxide (NOx) sind gasförmige Stickstoff-Verbindungen, die generell bei Verbrennungsvorgängen, aber auch durch natürliche mikrobiologische Abbauprozesse im Boden entstehen.
In der Stahlerzeugung entstehen Stickstoffoxide in Produktionsprozessen in Industrieöfen und in den Kraftwerksanlagen bei der energetischen Verwertung der Prozessgase. Durch Entstickungsanlagen und verbesserte Brennertechnologien konnte voestalpine diese Emissionen im längerfristigen Vergleich senken, die spezifischen NOx-Emissionen lagen 2015 bei 0,58 kg je Tonne Rohstahl.
Emissionsreduktion Uddeholms AB, Schweden
Vor der Umstellung auf Flüssiggas wurden Aufwärm- und Wärmebehandlungsöfen hauptsächlich mit Öl betrieben. Bis 2014 wurden alle Öfen auf Versorgung mit flüssigem Erdgas umgerüstet. Diese basiert auf einer modernen Brennertechnologie und ermöglichte in Kombination mit weiteren Prozessverbesserungen im Zuge der Umstellung insgesamt eine Reduktion des Energieverbrauchs um 28 GWh/Jahr sowie eine erhebliche Emissionsverminderung gegenüber der Vorgängertechnologie.
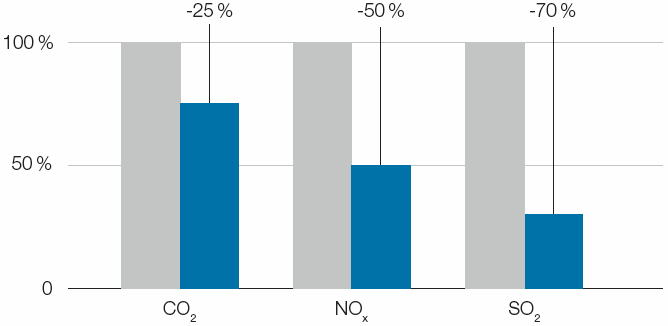
Staubemissionen
Staubhältige Abluft und Abgase, die in der Produktion anfallen, werden mit ebenfalls dem Stand der Technik entsprechenden Maßnahmen und Vorkehrungen erfasst und einer Entstaubungseinrichtung zugeführt.
Die spezifischen Staubemissionen waren 2015 mit 0,042 kg je Tonne Rohstahl gegenüber dem Vorjahreswert leicht rückläufig. Nach einer signifikanten Reduktion um mehr als 20 % von 2008 auf 2009 bleiben sie somit seitdem auf niedrigem Niveau.
Gefasste spezifische Staubemissionen
in kg/t Rohstahl
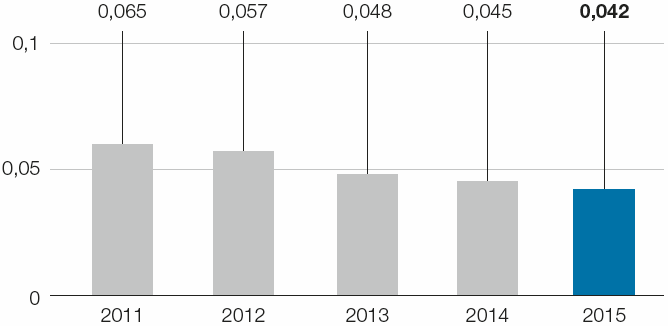
Direktreduktionsanlage in den USA
Die neue Direktreduktionsanlage in den USA gilt auch anlagentechnisch als Umwelt-Benchmark. Neben der Anwendung bester verfügbarer Technologien zur Emissionsminimierung in Luft und Wasser werden mittels einer Brikettieranlage anfallende Filterstäube und sonstige eisenhältige Produktionsrückstände für eine vollständige Rückführung in den Prozess aufbereitet („Zero-Waste“-Produktion bei maximaler Rohstoffeffizienz).
Entstaubungsanlage bei Buderus Edelstahl GmbH, Wetzlar, Deutschland
Im Elektrostahlwerk wurde Ende 2014 eine zentrale Entstaubungsanlage in Betrieb genommen. Die Absaugung erfasst neben den Elektroöfen auch andere Emissionsquellen und leitet diffuse Emissionen nicht ab. Sie zeichnet sich gegenüber den zuvor verwendeten Entstaubungseinrichtungen durch eine mehr als dreimal so hohe Absaugung und eine doppelt so hohe Reinigungsleistung aus.
Seite teilen