The major air pollutants that occur during the production of steel besides greenhouse gases (in particular CO2) are sulfur dioxide (SO2), nitrous oxide (NOx), and dust. Emissions of all of these pollutants comply with the statutory threshold limits. These parameters are measured regularly and the annual loads recorded; intermittent analyses are also carried out.
voestalpine makes every effort to minimize to the greatest extent possible the air pollutants that occur during production due to purely technical reasons related to the process. On one hand, this is done by way of optimization of the technical process (process integrated (PI) measures) and on the other, through end-of-pipe measures utilizing state-of-the-art technology.
Fundamentally, process-related emissions that result primarily from the raw materials required and from existing production processes cannot be avoided entirely because of technical limitations. Due to the environmental measures that were begun in the mid-1980s and continued since then with significant technical effort and financial expense, emission levels have practically reached the minimum that is currently technically achievable. Therefore, no additional significant reduction is possible with currently available technologies, as illustrated in the following.
For example, the specific emissions for CO2, SO2, and NOx in the last five years are within the production-based fluctuation range. During the last three decades, the specific emissions produced by the voestalpine Group (i.e., based on one ton of crude steel) have been reduced as follows: CO2 by 20%, SO2 by 75%, NOx by 27%, and dust by 95%.
CO2 emissions
Crude steel production using the LD process, which continues to be the worldwide standard in steel production, creates emissions from unavoidable chemical reactions that are process-related. In the production of pig iron, the raw materials coal and coke are needed in the blast furnace as reducing agents, while carbon is necessary in order to extract oxygen from the iron ore. Subsequently, the carbon still contained in the pig iron is oxidized in the LD converter by blowing in oxygen. Therefore, when carbon and oxygen combine, carbon dioxide (CO2) is created.
A reduction of these process-related CO2 emissions can only be achieved by way of partial (or in the case of total decarbonization) complete replacement of carbon, in other words, a completely new production process. (In this regard, see the chapter “Energy and climate policy”.) From today’s perspective, these technological options can only be realized over the long term due to their complexity.
As described above, the required use of carbon and the resulting CO2 emissions are already very close to the technically possible minimum threshold.
At the Linz and Donawitz locations, whose blast furnaces are among the best compared to other European countries, a total of 11.7 million tons of CO2 were emitted in 2015. This corresponds to specific CO2 emissions of 1.67 tons (based on one ton of crude steel); viewed against the comparative figures, the changes are within the production-based fluctuation range.
Specific CO2 emissions caused by voestalpine, reported in accordance with the Austrian Emissions Allowances Act (EZG)
t/t of crude steel
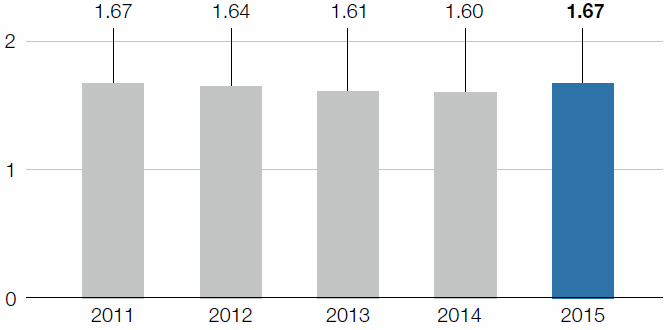
Figures refer to CO2 emissions pursuant to the Austrian Emissions Certificate Act at the Linz and Donawitz sites
By way of its applications (such as lightweight construction, improved efficiency in power plants, electric motors, renewable energy), high quality steel makes a significant contribution to the improvement of the energy balance sheet of these products, therefore improving the CO2 balance sheet as well. According to a study by the Boston Consulting Group, which was carried out on behalf of the German Steel Federation (“Steel’s CO2 balance sheet: A contribution to climate protection”), these applications save six times the amount of CO2 than is created during steel production.
Awards for climate protection
The production at our location in Zeltweg has been CO2-neutral since 2010; in 2014, it received the European EMAS Award for eco-innovations. In addition to measures to increase efficiency and reduce consumption, 75% of the heating of the plant was converted to biomass, and a small hydropower plant was installed on the Pöls River. voestalpine Tubulars Gmbh & Co KG in Kindberg received the klimaaktiv award for its comprehensive expertise in climate protection, especially with regard to energy efficiency, from the Austrain Federal Ministry for Land and Forest Management, Environmental and Water Management (less formally known as the Lebensministerium or Ministry of Life).
voestalpine Polynorm B.V., Netherlands
By using new compressors with a heat recovery system, almost 50,000 m3 of natural gas can be saved annually in the future, which means a reduction of CO2 output by 340,000 tons.
Specific SO2 emissions
kg/t of crude steel
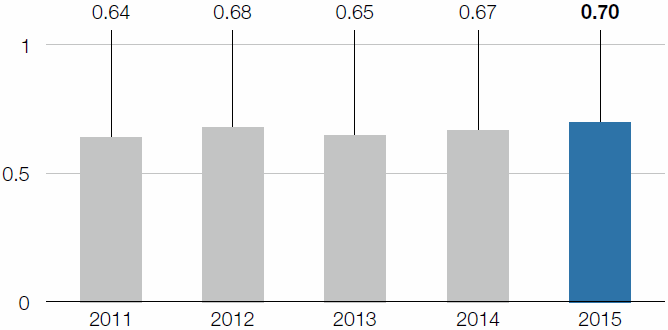
SO2 emissions
Many raw materials contain sulfur, which is then introduced into the production process. During certain processing steps and when by-products (coke oven gas and blast furnace gas) are used for energy generation, sulfur is released as sulfur dioxide (SO2).
The specific SO2 emissions in 2015 were 0.70 kg per ton of crude steel. In recent years, changes were within the production-based fluctuation range.
Specific NOX emissions
kg/t of crude steel
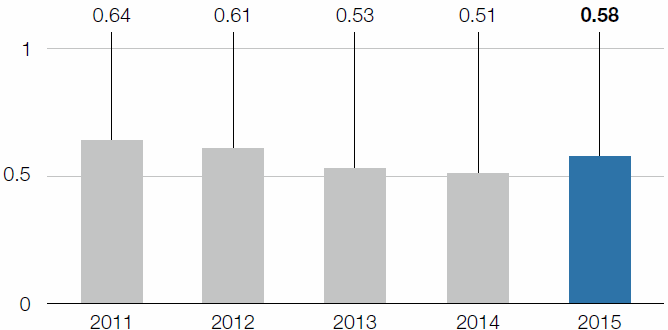
NOx emissions
Nitrous oxides (NOx) are gaseous nitrogen compounds that are generally created during combustion processes; they are also created in the soil through natural microbiological decomposition processes.
In steel production, nitrous oxides are created during the production process in industrial furnaces; they are also created in power plants when utilizing process gases for energy generation.
By deploying denitrification systems and improved combustion technologies, voestalpine has been able to reduce these emissions in a long-term comparison; in 2015, the specific NOx emissions were 0.58 kg per ton of crude steel.
Emission reduction at Uddeholms AB, Sweden:
Prior to switching to liquid gas, warm-up and heat treatment furnaces were powered mainly by oil. Until 2014, all of the furnaces were converted to burn liquid natural gas. This is based on a modern combustion technology and, combined with additional process improvements during the conversion process, it enabled an overall reduction of energy consumption by 28 GWh per year and a significant reduction of emissions compared to previous technology.
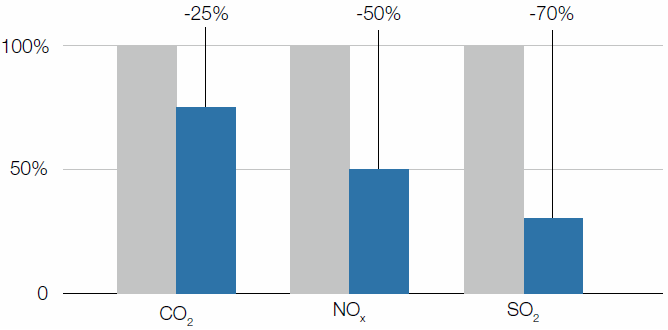
Dust emissions
Dust-laden exhaust gases and emissions that occur during production are captured and routed to a dedusting system by way of state-of-the-art measures and precautions.
The specific dust emissions were 0.042 kg per ton of crude steel in 2015, down slightly compared to the previous year’s figure. After a significant reduction of more than 20% between 2008 and 2009, they have remained at a low level.
Specific captured dust emissions
kg/t of crude steel
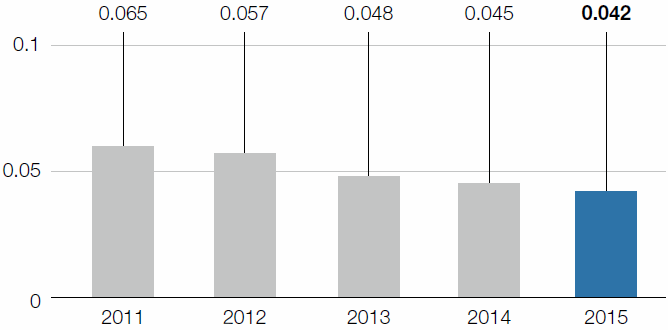
Direct reduction plant in the USA
The new direct reduction plant in the USA is also considered an environmental benchmark with regard to its technology and engineering. In addition to the use of the best available technologies to minimize air and water emissions, a briquetting plant processes filter dust and any ferrous production residue and recycles it back into the process (zero waste production with maximum raw materials efficiency).
Dedusting system at Buderus Edelstahl GmbH, Wetzlar (Germany)
A central dedusting system was put into operation at the electric-furnace steel plant in late 2014. Dust is extracted from the electric furnaces and other sources of emissions; diffuse emissions are not extracted. The extraction performance has been tripled compared to the previously used extraction system, and the cleaning efficiency has almost doubled.
Share page