SDG 3 – Good health and well-being
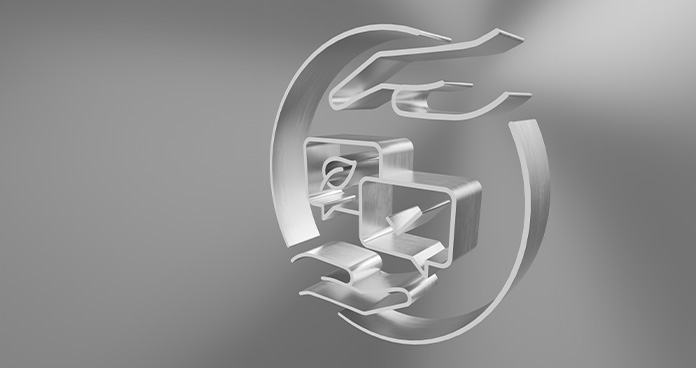
voestalpine’s health & safety values
Protecting its employees and their health is a central element of voestalpine’s Sustainability Strategy. What matters, day in and day out, is to implement the Group’s high standards at all facilities and refine them. We thus treat issues of health & safety with the same consistency and passion as we treat the quality of our products and processes. The “Safety is non-negotiable” safety code adopted in the business year 2023/24 clearly expresses this attitude. After all, sustainable success is only possible with healthy employees in a safe environment.
- Safety and health have the highest priority.
- Our executives stand for these core values, ensure consistent compliance with them, and assume leadership roles in doing so.
- Safe work practices (SWP) are a prerequisite for employment with voestalpine.
- Our employees’ personal conduct at the workplace affects everybody’s safety and health.
- Conscientious and responsible employees pay attention to themselves as well as to their co-workers.
- We also expect our contractors and partners to give priority to the safety and health of their employees.
- Healthy, unharmed employees are the foundation of a healthy and successful company.
- Every occupational accident is one too many and preventable.
OUR VISION: Zero workplace accidents and no occupational illnesses
The health & safety ORGANIZATION
The physical and mental health of all employees along with safety at the workplace are core voestalpine values. This is underscored by the fact that the corporate health & safety (h&s) unit reports directly to one of the members of voestalpine AG’s Management Board. It is run by the Chief health & safety Officer and fosters cooperation across the Group. This unit and a health & safety Committee, which consists of employees from all four divisions and one Works Council representative, collaborate intensely on lowering the frequency of accidents.
voestalpine’s health & safety unit continually fosters a health & safety culture that all employees throughout the Group embrace in practice. Aside from the Chief health & safety Officer, the h&s Board (comprising all Management Board members from all divisions), the h&s Committee, and managers in each division also have a role to play in this connection. Safety projects that serve to prevent accidents and strengthen people’s awareness of safety issues are carried out in all divisions. Special attention is also paid to safety leadership.
The voestalpine Group has defined the following safety standards:
- Every production company must put in place a safety system appropriate to its size and the nature of its activities.
- Safety audits are measures aimed at checking the lived reality of the safety culture and must be conducted by production company executives.
- Near misses must be reported, analyzed, and documented. Appropriate actions must be devised and implemented based thereon.
The effectiveness of the Group-wide safety standards is reviewed annually using a Web-based tool and improved as necessary through appropriate action.
voestalpine’s Management Board member responsible for workplace safety is required to perform annual safety audits in the given divisional entities. The given member of the executive management responsible for workplace safety at the defined entities is required to carry out quarterly safety audits. The lost time injury frequency rate (LTIFR) and the health status are the two key safety indicators that the companies compile uniformly throughout the Group.
LOST TIME INJURY FREQUENCY RATE
The LTIFR indicates the frequency of accidents based on the number of reportable workplace accidents entailing more than three sick days per one million hours of work performed. Given stark differences in the rules and regulations that apply in individual countries, the Group has established uniform definitions of reportable workplace accidents, sick days, and working hours.
The number of workplace accidents has dropped sharply in recent years thanks to consistent health & safety measures in the divisions. There were 633 reportable workplace accidents in the voestalpine Group during the business year 2023/24. Unfortunately, one voestalpine employee had a fatal accident.
In-person training courses on occupational safety were held at all locations, which explains the further decline in accident frequency in the business year 2023/24.
Development of the lost time injury frequency rate (LITFR)
As of the March 31 reporting date
The accident reports are recorded in a central database system for the purpose of carrying out event analyses and filing the information with the authorities. Appropriate improvement measures are adopted and communicated based on the findings of the event analyses.
The number of near misses is recorded in accordance with voestalpine’s safety standards using a Group-wide Web-based health & safety tool. If compliance at a facility with the required processes is insufficient, the facility must report planned improvement measures along with the envisioned completion date in this Web-based tool.
HEALTH STATUS
The health status shows the percentage of prescribed working hours during which all employees were actually present during a pre-defined period.
A high health status is not only good for the employees, it is also good for the company. It demonstrates the outcome of an effective health policy as well as the company’s responsible and respectful attitude toward its employees. No matter how important it is to achieve a high health status, it is equally important to ensure that employees do not come to work when they are sick.
Development of the health status
in %, as of the March 31 reporting date
OCCUPATIONAL health & safety AND HEALTH PROMOTION
voestalpine’s larger facilities (for example, Linz and Donawitz in Austria) have dedicated occupational health & safety centers that offer not only acute medical care, but also preventive care, physical therapy, vaccination campaigns, and psychological consulting. voestalpine’s employees can use this medical support structure to avail themselves of the company’s measures to promote employee health that surpass the statutory occupational health programs. At smaller facilities, occupational medical services are provided by select external partner entities.
There is no Group-wide guidance for such voluntary measures to promote employee health; instead, they are actively planned and carried out by the individual companies themselves. Such measures focus on movement and ergonomics; medical tests and exams; mental health; vaccinations; and healthy nutrition.
health & safety MANAGEMENT SYSTEMS
Absolutely all of voestalpine’s production companies (with 48,000 employees) have a health & safety management system, and 76% of them are certified pursuant to ISO 45001 or an equivalent, national health & safety standard. This means that some 38,500 employees (80%) working in production are employed at a facility that has a certified occupational safety system.
About 80% of the safety experts and/or health & safety officers are employees of voestalpine; at smaller facilities, external experts are hired to provide these services. voestalpine implements absolutely all laws pertaining to the protection of employees in all countries in which it works. In addition, compliance with the health & safety Group guideline adopted by the Management Board of voestalpine AG in April 2021 is mandatory.
This guideline regulates the following issues:
- Our health & safety values
- Group-wide safety standards
- Reality check
- Safety for new employees
- Implementation responsibility
Of the relevant companies, 90% will be certified under ISO 45001 (or an equivalent, national health & safety standard) by the business year 2024/25.
health & safety TRAINING
voestalpine Group companies regularly hold safety meetings with all of their employees. A meeting between the respective master craftsperson and their staff is scheduled monthly. The safety experts and health & safety officers at the production plants explain occupational safety rules and regulations during the monthly 15-minute safety training modules. These regular meetings, which are also attended by the Works Council, serve to discuss and adopt measures aimed at improving workplace safety. The frequency of the meetings is contingent on the size of the given company and the participation of people from various levels of the hierarchy. Furthermore, physical safety inspections are conducted once every quarter by management, including once per year with joint participation by members of the Management Board.
All employees are required to complete the health & safety training, which is available in 15 languages. Both voestalpine’s health & safety values and its safety standards are imparted in this online training, which supplements the face-to-face training.
These training sessions vividly demonstrate to employees how voestalpine’s safety culture is developed and practiced. Training sessions are also conducted for management and master craftspeople.
As of calendar year 2024, a safety calendar highlighting specific safety behaviors for each month will be available (digital and print version).
OCCUPATIONAL SUPPORT — FOCUS ON HEALTH
In the business year 2023/24, short presentations were once again given by occupational physicians and an occupational psychologist under the title “Focus on health.” This enabled 2,332 people to be reached at their place of work. The focus was on stress management and shift work.
A safety and health center was set up near the company medical center on the plant premises in Linz. Here, employees can learn first hand about safety- and health-related behavior at numerous stations to become more aware of hazards in the workplace. The center is committed to fostering health at the workplace and offers personal protective equipment, information on the correct handling of hazardous substances and tools, and a virtual crane runway.
The “COVID-19 Concerns Hotline” set up during the pandemic as a low-threshold contact point for all employees was retained and developed into a general “Concerns Hotline.” A clinical health psychologist is available for confidential discussions and also helps to find further support services during personal or health crises.
Another offer to promote more physical fitness in everyday working life is the online course “Strong back,” which is run twice a week by a qualified physiotherapist. A total of 2,503 people were reached in 66 sessions.
Presentations in 2023/24
Development of the total number of participants
As of January 16, 2024
WORKPLACE SAFETY AT CONTRACTORS/THIRD-PARTY ENTITIES
voestalpine also works to protect the health and safety of third-party employees. Binding guidelines, which the employees of contractors and third-party entities must comply with, have been issued to this end.
Both compliance with voestalpine’s safety standards and participation in safety training events are mandatory. At the company’s locations in Austria, all employees of third-party entities who have completed voestalpine’s safety training are given a badge that must be attached visibly to their clothing.
These training courses (Safety Training Environment; SATRE) are prescribed in the general terms and conditions for purchasing. Completion of these training courses is reviewed before the start of work and evaluated annually in the supplier assessment.
Temporary employees are treated the same as regular employees and are therefore also trained and instructed with respect to occupational safety.