SDG 3 – good health and well-being
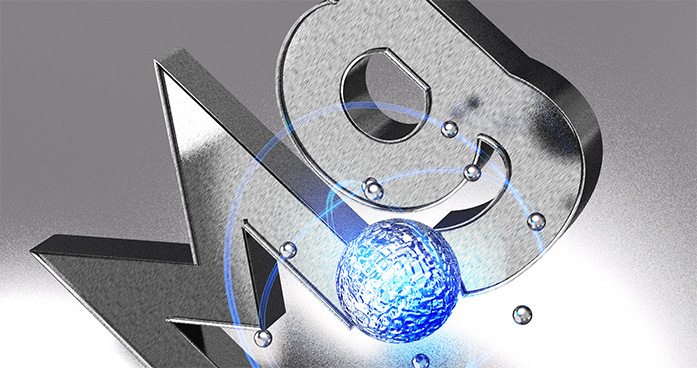
The health & safety (h&s) system
The Group’s employees are its backbone. Hence their physical and psychological wellbeing (health) and their security (safety) at the workplace are considered key values at voestalpine.
This is underscored by the fact that the Corporate health & safety department reports directly to one of the members of voestalpine AG’s Management Board. It is run by the Chief health & safety Officer and fosters cooperation across the Group. The department cooperates intensively with a health & safety Committee, which is made up of employees of all four divisions and Works Council representatives, to lower the frequency of accidents. The accident frequency rate has already been reduced by 30% since the department was established in 2015.
Within the voestalpine’s health & safety system, a health & safety culture is developed that all employees throughout the Group are expected to embrace. Aside from the Chief health & safety Officer, the h&s Board, and the h&s Committee, managers in each division also have a role to play in this connection. Safety projects that serve to prevent accidents and strengthen people’s awareness of safety issues are carried out in all divisions.
The following safety standards have been defined for the voestalpine Group:
- Every production company must put in place a safety system appropriate to its size and the nature of its activities.
- Safety audits are measures aimed at checking the lived reality of the safety culture and must be conducted by production company executives.
- Near misses must be avoided and documented by way of event analyses; appropriate actions must be devised in light of any such events and implemented.
The effectiveness of the Group-wide safety standards is reviewed annually using a Web-based tool. Targeted questions lead to an assessment based on a stoplight system (green/yellow/red). When matters are in the yellow or red zone, actions showing how the transition to green will be achieved must be put in place.
Starting in the business year 2018/19, the voestalpine Management Board member responsible for workplace safety has had to carry out an annual safety audit. The managing directors responsible for workplace safety at the production companies must carry out quarterly safety audits.
The Lost Time Injury Frequency Rate (LTIFR) and the health status are the two key safety indicators that the companies compile uniformly throughout the Group.
Lost time injury frequency rate
The LTIFR shows the number of reportable workplace accidents entailing more than three lost days per one million hours worked.
There are large differences in the definitions of reportable workplace accidents, lost days, and working hours in the individual countries in which voestalpine works. Hence a uniform definition was put in place at the Group level. It has governed the figures that have been collected since the business year 2015/16. As a result, the figures compiled before this date cannot be compared to the ones compiled after it.
Thanks to consistent health & safety measures in the divisions, the number of workplace accidents has fallen continuously in recent years.
In the business year 2018/19, not a single fatal work-related accident involving voestalpine employees occurred in the entire Group.
Development of the lost time injury frequency rate (LTIFR)
As of the March 31 reporting date
Learning from each other:
Examples of how to lower the LTIFR
Just as in 2018, this year too the safety experts of all four divisions were invited to share their experiences during the so-called health & safety Days. The first-ever separate event for European safety experts who do not speak German was held in Düsseldorf in May 2019. The German-speaking safety experts met in Leoben in June 2019.
“Learning From Each Other” and “Developing a Strong Safety Culture” were the events’ mottos. At both events, Group companies were audited, and positive examples from the divisions were introduced and given the Committee’s health & safety Award.
Six best practice examples among others were honored at the health & safety Days in Leoben. The “One Step Ahead—Get Home Safely” campaign of voestalpine Rotec GmbH is but one example. Small groups were formed to engage in discussions with employees and educate them about workplace safety.
Health status
The health status shows the percentage of prescribed working hours during which the employees are actually present in a predefined period.
A high health status is not only good for the employees, it is also good for the company. It demonstrates the outcome of an effective health policy as well as the company’s responsible and respectful attitude toward its employees. No matter how important it is to achieve a high health status, it is equally important to ensure that employees do not come to work when they are sick.
Development of the health status
As of the March 31 reporting date
ISO 45001
Many voestalpine Group companies have already been certified under an occupational safety and health management system.
The certification pursuant to the new international ISO 45001 standard is carried out in connection with recertifications pursuant to OHSAS 18001.
Workplace safety at contractors / Third-party companies
voestalpine also endeavors to protect the life and health of third-party employees.
Binding guidelines that the employees of contractors and third-party companies must comply with have been issued to this end.
Share page