In the past business year, the voestalpine Group invested EUR 140.3 million in research, development, and innovation and thus – as in previous years – continues to be one of the most research-intensive companies in Austria. For one, the focus of our research is on further developing the steel production process and the manufacturing processes for steel and other metals, including the development of new production techniques such as additive manufacturing, and secondly on materials technology as well as the development of metal-based products, components, and complete system solutions.
The average annual 4.3% increase in R&D expenditures over the past years indicates that innovation is given top priority in the voestalpine Group. The research ratio (proportion of R&D expenditures in relation to revenue) remained unchanged at 1.2% and the R&D coefficient (expenses measured by added value) at 2.7%.
Research expenditure for the voestalpine Group
In millions of euros, R&D gross expenditure (without R&D facility investments)
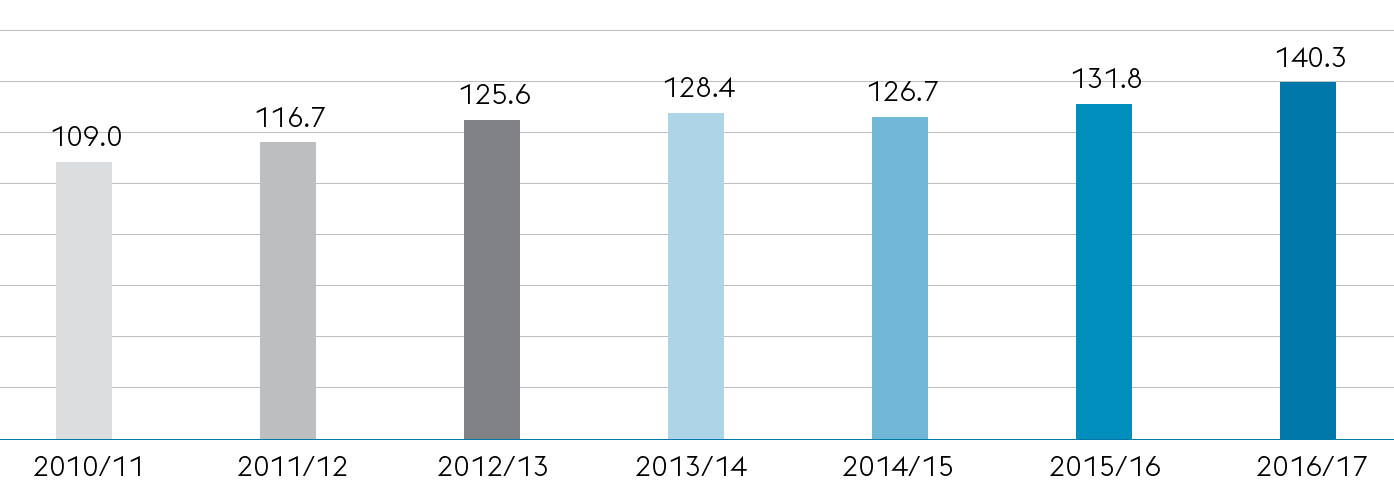
Our continuous cooperation with around 80 universities and research institutions worldwide, and, with that, the close interaction between research, science and industry forms the basis for the constant advancement of most sophisticated high tech metal products. Major research partners in Austria include the Montan University in Leoben, the Johannes Kepler University in Linz and K1-MET GmbH in Linz. Abroad, focus projects with MIT (Massachusetts Institute of Technology), USA, McGill University, Canada, the Royal Institute of Technology, Sweden, Aalto University, Finland and the Fraunhofer Institut, Germany, are ongoing.
Research work at voestalpine is decentralized, i. e., conducted in close vicinity to the relevant production facility as well as to customers and the market. In order to ensure continuous knowledge exchange within the Group besides regular Research Committee meetings where representatives responsible for R&D from the four Divisions share information and coordinate activities, the Research Board with the participation of the Management Board convenes twice a year and decides on fundamental issues regarding the Group’s innovation developments. In addition, a one-and-a-half day Researcher Conference is held once a year with 2017 marking its tenth anniversary. This year’s topic “Steel Production in the 21st Century” was discussed in detail in presentations from external and internal experts. At the location in Linz, Austria, a pilot project for hydrogen production was started and involves the strategic cooperation between voestalpine and VERBUND AG, the leading electricity producer in Austria. The focus here is the installation of the largest PEM (polymer electrolyte membrane) electrolysis unit worldwide with an output of 6 MW to produce “green” hydrogen, i. e., by using electric energy from renewable sources. The objective of this project is to test the PEM technology as well as reveal the potential of hydrogen in steel production. The use of this technology in the steel industry seems promising for the long-term future, but ultimately depends on the cost and availability of “green” power.
Research and development in the Steel Division are ever more strongly shaped by the need for flexible, autonomously controlled processes in terms of digitalization with a pronounced focus on the development of mechatronic systems as the basis for “smart production”. The emphasis in the area of material technology is on the further development of ultra high-strength steel grades both for cold-rolled and hot-rolled steel strips as well as the development of more high-ductility grades – high-strength steels with increased formability – in combination with the relevant processing technologies, and especially in cooperation with the Metal Forming Division. The newly developed heavy plate sheet product toughcore® with its superior ductility properties was successfully launched and is used for challenging projects under the harshest conditions, such as in mining and linepipe offshore applications. In the coatings segment, the focus is on the development of alternative metal coatings and innovative organic coatings with integrated functionalities.
In its value added service developments, i. e., heat treatments, coatings and processing, the High Performance Metals Division (formerly Special Steel Division) relies increasingly on customer proximity and is thus expanding its global presence primarily in Asia in cooperation with other local R&D centers. In the summer of 2016, the voestalpine Additive Manufacturing Center was opened in Düsseldorf, Germany, to pool all Group-wide research activities in this field and develop techniques to manufacture special complex and light metal components – particularly for the aerospace and automotive industries as well as for toolmaking. The material required for the process – a metal powder produced using a special method – is developed and supplied by the Group companies Böhler Edelstahl GmbH & Co KG, Austria, and Uddeholms AB, Sweden. The High Performance Metals Division invests heavily in the digitalization of production as well with the goal to further increase production efficiency and product quality on a large scale. In the tool steel segment, a powder-metallurgical steel was recently developed that combines the previously incompatible properties of high-corrosion resistant but formable steel with the ductility and wear resistance of tool steel. Another innovation includes non-corrosive, pre-hardened steels for tool holders that significantly shorten the production route, lower production costs and time, and accelerate deliveries. Furthermore, this innovation eliminates the complex and environmentally critical chemical nickel plating of the tool holders.
In the previous year in the Metal Engineering Division, a research service company was founded to ensure optimal use of the research infrastructure and R&D processes were reorganized at the same time. voestalpine is the only turnkey supplier for rail technology and turnout systems worldwide. With these two segments, the division offers new cutting-edge system solutions for the railway infrastructure that also include an interactive life cycle cost tool developed by voestalpine Schienen GmbH, Leoben/Donawitz, Austria, for life cycle analyses of high performance rails to optimize procurement and maintenance strategies and facilitate cost projections over the entire life cycle. The newly developed rail grade 400 UHC® HSH®, a heat-treated rail with increased carbon content, exhibits twice the rail service life compared to previous grades and thus has had a very positive market response. Digitalization was the central focus for the recently developed turnout systems with continuously optimized integrated diagnostic and monitoring technologies. Other R&D priorities of the division include the development of high-strength thermomechanically rolled wires as well as sour gas-resistant seamless tubular products and gas-tight connections, in particular for geologically and climatically challenging oil and gas exploration and production applications.
With the creation of twelve centers of excellence in the Metal Forming Division, R&D structures were comprehensively redefined and reorganized accordingly. The primary focus in this division is on innovative lightweight structures. This segment includes the forming and further processing of materials such as press-hardening steel, steel hybrid composites or aluminum into components and systems with the goal to maximize customer benefit by combining best-suited materials. Another priority for the division is the development of innovative, sophisticated profiles and pipes made from high-strength steel combined with metal coatings and plastic film or steel-plastic composites.
Share page