At EUR 109.0 million, the voestalpine Group maintained its expenditures for research and development in the business year 2010/11 at the previous year’s very high level (EUR 108.8 million). Due to ongoing improvements in efficiency, including in the area of R&D organization, actual expenditures were slightly lower than the available R&D budget of EUR 110.8 million, although all of the planned projects were implemented throughout.
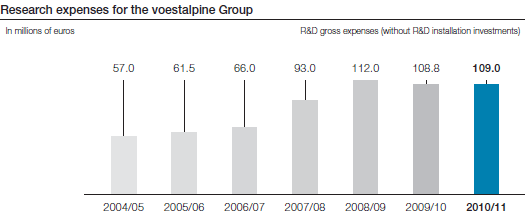
The budget approved for the current period of 2011/12 provides for an additional increase of technology and innovation funding by 10%, thus bringing it to a record high of more than EUR 120 million. The budget in all five Group divisions will reflect this increase, with the Special Steel Division showing the most substantial growth at about 25%.
The research ratio of the voestalpine Group (share of R&D expenses in total sales) at the end of the business year 2010/11 was 1.0% (previous year: 1.27%), the R&D coefficient (funds measured by economic value added) is 2.55% (previous year: 3.42%).
Focal points of ongoing R&D activities
The focus of research and development activities is on cross-divisional long-term projects in the mobility and energy sectors, which already represent the two largest customer segments of the voestalpine Group.
In addition to further development of lightweight materials for the automotive and consumer goods industries, the focus is on technologically highly sophisticated applications in the energy sector, such as high-temperature materials, which enable significantly higher efficiency in power plant turbines and aircraft engines than was previously possible. Another focal point is innovation in the renewable energy sector; here, it is the long-term goal of the voestalpine Group to position itself in the top technology and quality segment.
Viewed Group-wide, the R&D segment is aiming for an optimum combination of material, tools, and processing. For example, in the past business year, voestalpine Stahl GmbH was awarded the innovation prize of a leading automotive journal for a steel and aluminum hybrid blank for the automotive industry, which it developed jointly with an industrial partner. The particular innovation in the combination of these two very different materials is that, after the assembling process, the hybrid blank can be formed into components. Currently, concrete applications are being defined jointly with customers from the automotive industry.
The focus in the sectors of rail and turnout technology is in the long-term expansion of the Group’s global technology leadership as well as in the continuing sustainable optimization of the life-cycle costs of innovative complete solutions. For example, the past business year saw a pilot run using a specially developed switch drive system that integrates all the required functions, such as switching and monitoring, which took place on a new high-speed line in Korea with speeds of up to 370 km/h.
With the launch of the Steel Innovation Center at the Group’s Linz site, voestalpine took another step toward a long-term expansion of the Group’s leadership role in both technology and quality. The opening of the new laboratory center was in September 2010.
It is focused on the development of new surface technologies for high-quality steel coil, including underlying analytics, and it does not represent merely an isolated research center but is directly associated with the “Steel Development Center” (focus: material development) and the “Steel Processing Center” (simulation and optimization of processing steps, such as welding, pressing, and forming), which were established at the Linz site some time ago.
In the areas of recycling and zero-waste production, a research project is currently being realized jointly with the University of Mining and Metallurgy in Leoben within the scope of the Austrian federal government’s competency center program. The centerpiece of the project is a reactor that reclaims metal from metallurgical filter dust. The facility’s purpose is to make the process ready for industrial implementation.
Currently, the voestalpine Group is collaborating with more than 80 research and development partners all over the world that include both university research institutions and institutions closely associated with universities. The current deepening and expansion of such collaborations is therefore an important focus of our long-term innovation strategy. For example, the recent R&D collaboration in the area of surface and nanotechnology within the scope of the new cooperative project “SteelCoatingDesign” with the Johannes Kepler University was expanded. The main focus is on the development of innovative coatings.
As far as international R&D partnerships are concerned, it deserves special mention that voestalpine will be collaborating with the Advanced Steel Processing and Products Research Center at the highly regarded Colorado School of Mines, USA, as one of their corporate sponsors. Numerous projects relative to the further development of high- and ultra-high-tensile steel, which are particularly relevant for the voestalpine Group, are currently being undertaken at this institution.